Brief description
The operational conditions of district heating systems are subject to a constant change, e.g. due to decreasing specific heat consumption along with energy-efficiency retrofits or refurbishments of existing buildings (Energieeinsparverordnung EnEV; German energy savings regulations for buildings). As a result, district heating systems must be adjusted to the new operational requirements. An improved chilling of the district heating water supports this adjustment and enables a decrease in temperature levels on the primary side, reduces heat distribution losses, supports the integration of lower-tempered (waste) heat sources and improves heat supply at source.
Currently, there are partially essentially higher operational temperatures and exergy levels available on the primary side than required on the secondary side. This applies independently from the insulation standards and the efficiency of customer secondary heating systems connected to a district heating system. While, on the secondary side, temperatures higher than 70 °C are required for providing hot potable water and heating, temperatures can range from 80 °C up to 130 °C on the primary side. This exergy shall be used to power an absorption heat pump by the working pair ammonia water. The heat pump shall be integrated into existing district heating substations; as a result, the efficiency of the district heating system will increase.
Function description
The refrigerant is available in gaseous condition of aggregation in front of the absorber (1). The refrigerant gas is exposed to the weak solution (14) in an absorber, resulting in the refrigerant’s absorption. In this process, the refrigerant’s enthalpy of evaporation is released; therefore, heat must be extracted at a medium temperature level. This heat is part of the net power. After the absorber, the mixture of refrigerant and weak solution has an increased ammonia mass fraction and is in liquid condition (2). This mixture is described as strong solution – rich in ammonia. Via a solvent pump, the strong solution is adjusted to the system’s high pressure level (3). In a generator, heat at a high temperature level is transferred into the system. Thus, the strong solution is separated into a refrigerant vapor and a weak solution. This heat is extracted from the flow line of the district heating system. Due to the partial evaporation of the strong solution (6), the substance separates into refrigerant vapor (10) and weak solution (7). The latter is fed back to the absorber and reused for absorption. In order to increase efficiency, a solvent heat exchanger is used for inner heat recovery between strong solution (3→4) and weak solution (7→8).
The refrigerant from the generator is no pure ammonia due to its bonding with water. In order to increase the refrigerant’s purity, the vapor is partially condensed in a dephlegmator. In this process, water is predominantly separated and accumulates in the liquid phase. The refrigerant vapor (10) is subsequently condensed in the condenser at the temperature level of the secondary flow; a part of the useful heat is extracted from the process. Via an expansion valve, the liquid refrigerant’s pressure is reduced to the low pressure of the heat pump (12→13). Due to the expansion, a part of the refrigerant evaporates resulting into a temperature reduction. At the low pressure level, the refrigerant can be evaporated at a more reduced temperature (13→14). This effect is used in the evaporator in order to extract more heat from the district heat return flow and therefore to achieve the return flow’s temperature reduction. The refrigerant heat exchanger (RHX) as well as the solvent heat exchanger (SHX) increase the efficiency in the process: the refrigerant vapor (14→1) is superheated and the liquid refrigerant is supercooled after the condenser (10→11).
Objectives
By the use of the absorption heat pump within the district heating substation, the provided useful heat flow and the exergetic degree of efficiency shall be essentially increased. Operating this aggregate shall result into an essential reduction of the return flow temperature on the primary side. Furthermore, the absorption heat pump is to be optimized regarding the total heat input into the heat distribution system on the secondary side but also regarding the efficiency of the district heating system.
Project duration
November 2017 - April 2020
Project partners
Acknowledgements
This project is funded by the German Federation of Industrial Research Associations (AiF). The authors would like to sincerely thank for their support.
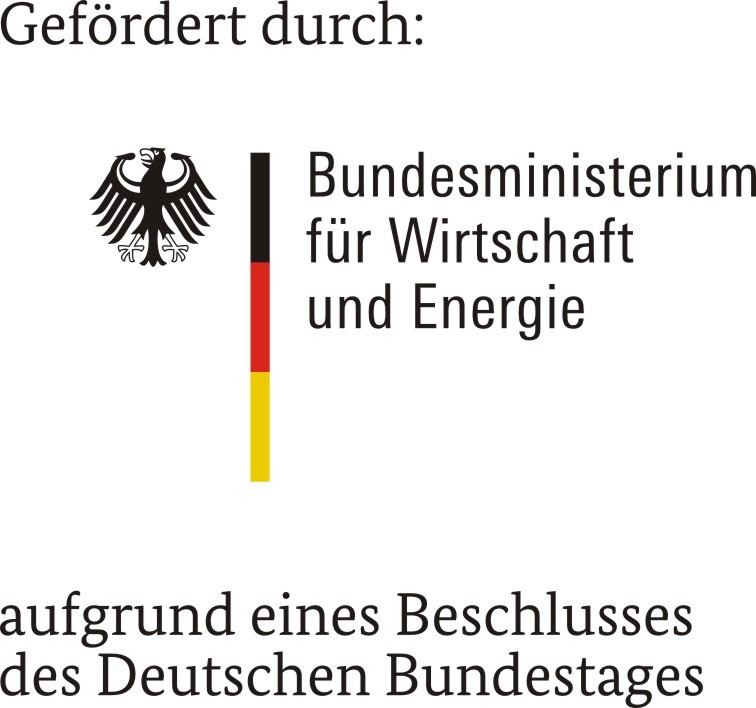

Contact
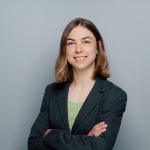
Luisa Haak, M.Sc.
Academic employee