Heat exchangers are core components of energy engineering systems, process engineering systems, refrigeration systems as well as thermal energy systems. Modern high-performance heat exchangers cannot be modeled in 3D or can only be modeled in 3D with considerable effort due to complex structures. In contrast, 1D calculation methods, such as using simplifying key figure charts (NTU charts), offer the possibility for a rough calculation of the heat exchanger. However, the achievable accuracy by such charts is partially considerably restricted due to simplifying assumptions.
An alternative to 1D and 3D modeling is the cell method (cell modeling): The heat exchanger is discretized in elementary cells of any desired dimensions. These elementary cells are flown through by heat absorbing media and heat emitting media, either in direct current, countercurrent or cross current. The specific characteristics of the cell areas are assumed to be known, such as heat transferring surface, heat transition characteristics or pressure loss characteristics. Based on known laws of physics, the thermal performance of each cell can be described via model equations. Solving these model equations for all cells in their entirety results in the thermal behavior of the entire heat exchanger. In cell modeling, local effects such as fouling or surface enlargement measures (finned surfaces) can be included.
Contact
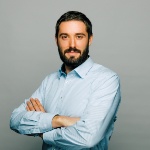
Lukas Siebler, M.Sc.
Academic employee